3.3.2. Проверка отдельных подсистем и элементов
После проверки правильности монтажа при условии завершения всех монтажных работ осуществляется проверка отдельных элементов системы и их готовность к совместной работе.
Эта проверка производится в следующем порядке. К проверяемому устройству подключают источник питания (по постоянной или временной схеме). При этом, если отсутствуют коммутационные аппараты, все непроверяемые подсистемы и элементы должны быть надежно отключены от общего источника питания, а тумблеры и переключатели проверяемых элементов установлены в положение «Выключено». Для проверки используют имитаторы и контрольные устройства.
Системы контроля проверяют, как правило, при трех значениях контролирующего параметра (минимальном, среднем и максимальном), а погрешность определяют при среднем значении измеряемого параметра. При необходимости с помощью органов настройки подрегулируют минимальное значение параметра и диапазон измерений. Инерционность измерения определяется как время между ступенчатым изменением значения величины на входе системы и моментом достижения этого же значения на отсчетном устройстве прибора.
При опробовании систем регулирования устанавливают среднее значение задания регулятору и имитирующим устройством изменяют значение регулируемого параметра в окрестностях заданного. При переходе значения регулируемой величины через заданное, управляющий сигнал регулятора должен переместить регулирующий орган в сторону, компенсирующую это изменение. Если регулирующий орган перемещается в противоположную сторону, изменяют фазировку системы регулирования и производят статическую настройку, обеспечивающую заданное проектное соотношение регулируемых величин во
всем диапазоне изменения технологических параметров.
При проверке систем дистанционного управления также проверяют правильность фазировки элементов. При этом снимают механические характеристики регулирующих органов — зависимость между перемещением клапана или заслонки и значением управляющего сигнала на входе исполнительного механизма. Для большинства регулирующих органов механическая характеристика должна быть прямолинейна.
При проверке систем управления, защиты и сигнализации преобразователи настраивают на предельные (согласно проекту автоматизации) значения параметров. При имитации возрастания или
уменьшения значения параметров до предельных значений должны работать все элементы системы. На практике исполнительные механизмы (особенно технологического оборудования большой мощности) часто монтируют и налаживают другие организации (монтажники-электрики). В этих случаях наладчики систем автоматизации совместно с ними должны проверить появление сигналов в цепях управления и защиты всего комплекса. Все обнаруженные и ликвидированные неисправности, механические характеристики регулирующих органов и другие сведения, необходимые для дальнейшего выполнения работ, фиксируют в журнале производства наладочных работ.
3.3.3. Наладка устройств контроля температуры
Порядок проверки и настройки систем автоматического контроля, сигнализации и защиты рассмотрим на примере простейшей системы автоматики приточно-вытяжной вентиляции с подогревом (рис. 3.3.1), выполненной на основе измерителя-регулятора типа ТРМ 12 .
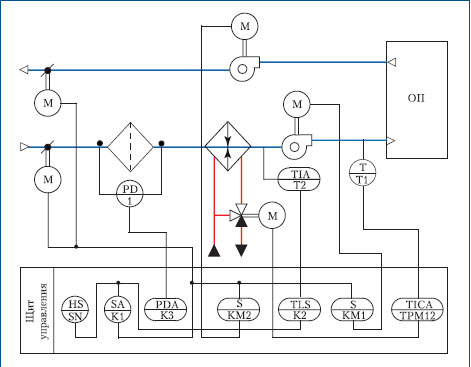
Измерение температуры осуществляется с помощью термопреобразователя Т1 сопротивления ТС 100П, подключенного на вход измерителя-регулятора ТРМ12.
В рассматриваемом примере применен датчик ТС 100П, подключенный по трехпроводной схеме с градуировочным сопротивлением соединительных проводов 15 Ом. Номинальная статическая характеристика датчика в диапазоне температур от 0 до 100 °С приведена в табл. 3.3.1.

Проверка элементов схемы измерения, как правило, выполняется двумя наладчиками, один из которых находится у термопреобразователя сопротивления, а другой — на месте установки вторичного прибора. После подачи питания на ТРМ 12 (включение автоматического выключателя F3) при исправности цепей и
источника сигнала на цифровом индикаторе в двух левых разрядах на некоторое время отобразится код датчика (для рассматриваемого типа — 03). В случае несоответствия кода, согласно инструкции по эксплуатации ТРМ 12, необходимо установить требуемый код. Сняв питание с ТРМ 12, отключают проводники соединительной линии датчика.
Линию в месте отсоединения датчика надежно закорачивают. Затем с помощью калибратора сопротивлений (например, ИКСУ-2000) попарно измеряют сопротивление между концами проводов, предварительно их промаркировав Rа, Rb, Rc. Сопротивление измерительных проводов определяется как
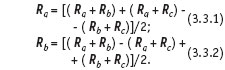
Определив сопротивление измерительных проводов Rа и Rb, подбирают сопротивление подгоночных катушек (путем намотки манганинового провода), чтобы сопротивления проводов вместе с катушкой были равны и не превышали половины номинального сопротивления линии (7,5 Ом).
Далее, для проверки основной погрешности, вместо датчика подключают калибратор термосопротивления (например, ИКСУ-2000, настроенный на термосопротивление ТС 100П) по схеме, показанной на рис. 3.3.3.
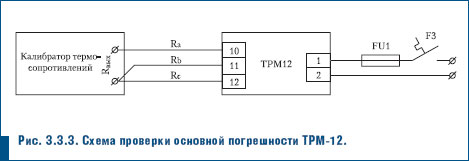
После подачи питания и прогрева приборов калибратор термосопротивлений последовательно устанавливают на значение сопротивления имитатора датчика, соответствующее температуре 0, 20, 40, 60, 80 и 100 °С, а затем меняют последовательность.
Значение показаний прибора в каждой точке заносят в протокол проверки, а затем вычисляют основную погрешность по зависимости (3.2.3). Основная погрешность для каждой точки не должна превышать ±0,5 %. Если по всей шкале наблюдается равномерное завышение или занижение измеряемой величины,
необходимо произвести калибровку прибора при уставке сопротивления, равной сопротивлению датчика при 0 °С. После перехода прибора в рабочий режим необходимо убедиться, что основная относительная погрешность находится в нормированных пределах (±0,5 %).
После включения прибора в работу на действующем оборудовании проверяют точность измерения по показаниям термометров, установленных по месту, или образцовых термометров, например ртутных. Если в процессе эксплуатации прибор показывает температуру, соответствующую верхнему/нижнему пределу измерения, то при исправности вторичного прибора это соответствует обрыву/короткому замыканию во внешних цепях*.
Чаще всего обрыв цепи появляется в местах соединения кабелей в переходных коробках, на клеммах щитов и самих термопреобразователей.
Причинами завышенных или заниженных показаний прибора может быть также влияние электрических и магнитных полей на соединительные линии. В этом случае проверяют качество заземления защитных труб, экранов и приборов. Сдаточные испытания по системам контроля, как правило, не проводят. Их сдают по результатам удовлетворительной непрерывной работы систем в течение трех и более суток.
3.3.4. Настройка устройств сигнализации и защиты
В рассматриваемом примере (рис. 3.3.2) предусмотрены:
- защита от замораживания на базе термостата Т2;
- блокировка работы системы при срабатывании пожарной сигнализации ПС;
- световая сигнализация при загрязнении фильтра на базе дифференциального реле давления РД1.
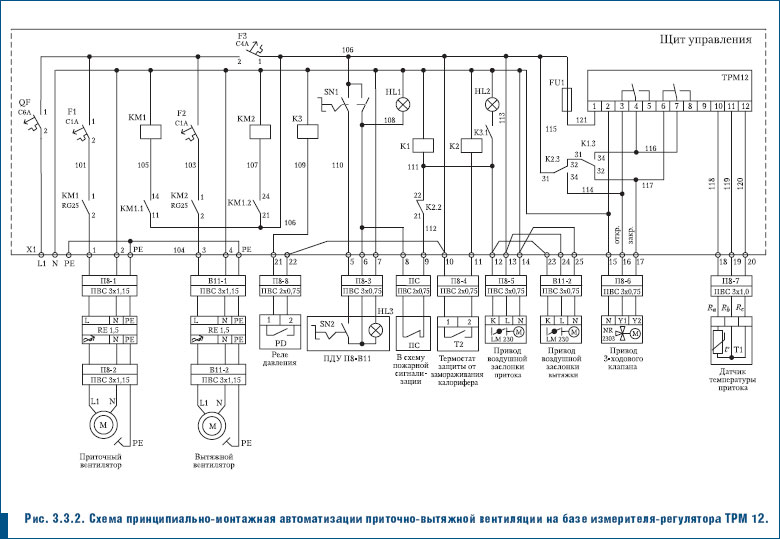
Настройку выполнения перечисленных функций начинают с проверки коммутационных элементов — электромагнитных реле К1, К2, К3.
При отключенном питании щита управления (автоматический выключатель QF) проверяют сопротивление катушек (должно быть несколько десятков Ом), легкость перемещения якорей реле и отсутствие перекоса. Якорь должен плотно и без зазоров прилегать к сердечнику. Катушки реле не должны иметь видимых повреждений, а контакты реле — следов коррозии. Если используется реле в герметичном корпусе, проверяется только сопротивление катушек. Затем, отключив питание двигателей вентиляторов (автоматические выключатели F1 и F2) и отсоединив приводы трехходового клапана и воздушных заслонок (клеммы 12, 13, 14, 15, 16, 17, 23, 24, 25), подают питание на цепи управления автоматическим выключателем F3 и переключателем SN1. При этом загорается лампочка HL1, сигнализирующая включение всей системы.
Проверку срабатывания устройств защиты и сигнализации проводят путем последовательной имитации срабатывания соответствующих датчиков. Обычно, в простейших системах, это производится закорачиванием или отключением клемм, к которым подключены датчики-реле. Для этой цели можно использовать устройство, собранное на основе тумблеров или переключателей.
При имитации срабатывания термостата защиты от замораживания Т1 (закорачивание клемм 10 и 11 на клеммнике щита управления) необходимо проверить выполнение следующего:
- подачу напряжения на катушку реле К2 (напряжение между L1 и клеммой 11 должно быть 220 В);
- размыкание контакта К2.2 (отсутствие напряжения между L1 и клеммой 9), что обесточивает катушку реле К1;
- переключение контакта К2.3 (наличие напряжения в 220 В между клеммами N и 16), подающего сигнал на полное открытие трехходового клапана и закрытие воздушных заслонок;
- размыкание контактов К1.1 и К1.2 в цепи катушек пускателей КМ1 и КМ2 (отсутствие напряжения между клеммой N и электрическими точками 105 и 107), отключающих двигатели вентиляторов.
При размыкании клемм 10 и 11 схема должна вернуться в исходное состояние. Имитация срабатывания защиты от замерзания непосредственно от датчика Т2 не производится из-за сложности искусственного создания в воздуховоде требуемой температуры (5,0-12,0 °С). На указанную температуру датчик-реле Т2 настраивается с помощью регулятора, выведенного на панель управления.
Имитацию срабатывания реле давления производят закорачиванием клемм 21 и 22. При этом:
- проверяется наличие напряжения на катушке реле К3 (между клеммами L1 и 22);
- проверяется срабатывание контакта реле Р3.1 (должна загореться лампочка HL2, сигнализирующая загрязнение фильтра).
Настройка реле давления РД осуществляется с помощью зубчатого лимба на передней панели датчика, проградуированного в миллибарах или паскалях. Значение давления срабатывания выбирается по характеристике конкретного фильтра в зависимости от пропускной способности системы (рис. 3.3.4).
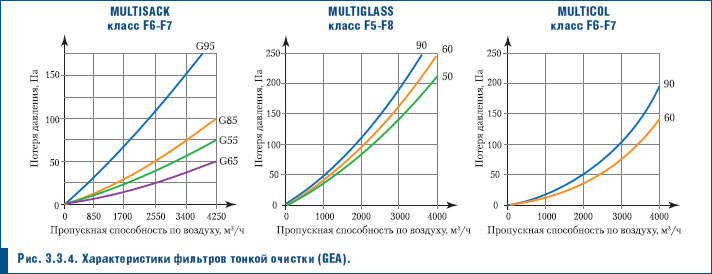
Проверку срабатывания пожарной сигнализации обычно проводят после отладки всей системы. Размыкание контакта ПС должно привести к потере напряжения на катушке реле К1 и, как следствие, к отключению вентиляторов и закрытию воздушных заслонок.
3.3.5. Проверка систем автоматизации при опробовании технологического оборудования
На этом этапе работ все подсистемы и элементы, от которых зависит безопасность и безаварийное ведение технологического процесса, должны быть включены в полном объеме. В первую очередь к этой категории относятся системы технологической и аварийной сигнализации, блокировки и защиты. Здесь главная задача наладчика — обеспечить пуск технологического оборудования и не допустить выхода средств автоматизации из строя в момент их включения. Поэтому опробование технологического оборудования должно производиться только по согласованию и с участием наладочной организации. В свою очередь, наладчики должны помнить основное правило работы на действующем оборудовании: все
технологические переключения, необходимые для наладки и испытания систем, должны производиться только технологами или по согласованию с ними и в их присутствии.
Включению системы автоматизации предшествует выполнение ряда требований:
- закрывают корпуса приборов и других средств автоматизации;
- подают питание на распределительные устройства системы автоматизации по постоянной схеме;
- проверяют параметры окружающей среды (температура, влажность, состав) в местах установки приборов, щитов, пультов на соответствие их условиям, допустимым для данного типа приборов;
- устанавливают предохранители, производят установку автоматических выключателей и настройку другой предохранительной аппаратуры в строгом соответствии с проектом автоматизации.
Включение систем автоматизации начинают с подачи питания на все первичные и вторичные приборы. Преобразователи и первичные приборы включают на измерение в соответствии с правилами, изложенными в инструкциях по монтажу и эксплуатации. При этом в случае необходимости органами регулируют нулевое значение измеряемых величин.
Перед включением приборов на непосредственное измерение необходимо убедиться в том, что характеристики реальных измеряемых сред (агрегатное состояние, температура, давление, влажность) близки к проектным. Например, в системах СКВ это производится с помощью местных измерительных приборов прямого действия (манометрические измерители температуры и давления), которые установлены непосредственно на технологическом оборудовании или линиях его обвязки.
Затем проверяется работа систем автоматизации в различных режимах. При этом переключение технологических режимов производится совместно с технологами или операторами технологического оборудования.
Если в период пуска или опробования система выходит из строя, то устраняют неисправности и перед повторным включением ее элементы снова проверяют. Сведения о результатах работ по включению систем автоматизации также заносят в журнал производства наладочных работ.
3.3.6. Наладка и испытание вентиляционных сетей
3.3.6.1. Испытание вентиляторов
Испытание вентиляторов осуществляют для проверки соответствия фактического режима его работы характеристике по каталогу и расчетным данным. Для установления фактического режима работы вентилятора определяют:
- перемещаемое количество воздуха, Lф (м3/час);
- полное давление, развиваемое вентилятором Рп (кПа);
- частоту вращения колеса вентилятора n (мин-1);
- мощность, потребляемую вентилятором N (Вт).
Подачу вентилятора определяют в сечениях до и после него. При испытании вентилятора с двухсторонним всасыванием его подачу определяют замерами расходов на прямых участках линии нагнетания. При достаточной герметичности камеры, в которой расположен вентилятор, расход воздуха на всасывании определяют на прямом участке всасывающих воздуховодов.
Полное давление, развиваемое вентилятором при его испытании в сети, находят как разность полных давлений на нагнетании и всасывании. Давление до и после вентилятора замеряют в плоскости фланцевых соединений всасывающего и нагнетательного патрубков центробежных вентиляторов или у фланцевых соединений всасывающего и нагнетательного воздуховодов для вентиляторов, установленных в воздуховоде.
При испытании вентилятора с двухсторонним всасыванием его подачу определяют замерами расходов на прямых участках линии нагнетания. При достаточной герметичности камеры, в которой размещен вентилятор с двухсторонним всасыванием, расход воздуха на всасывании определяют соответствующими измерениями на прямых участках всасывающих воздуховодов до камеры.
Мощность на валу вентилятора Nв определяется по формуле:

где Nэл — мощность, потребляемая электродвигателем, кВт;
э и п — КПД электродвигателя и передачи соответственно.
Перед сопоставлением фактического режима работы вентилятора с данными по каталогу необходимо величину замеренного полного давления, развиваемого вентилятором, привести к стандартным условиям воздуха (при давлении 760 мм рт. ст., температуре 20 °С, относительной влажности 50 %), используя формулу:

где Рф — измеренное полное давление, приведенное к стандартным условиям воздуха, кгс/м2;
Рп — измеренное полное давление, кгс/м2;
760 — барометрическое давление стандартного воздуха, мм рт. ст.;
Рб — измеренное барометрическое давление, мм рт. ст.;
t — измеренная температура воздуха, °С.
Если точка на графике (рис. 3.3.6), определяемая фактической подачей Lф и фактическим полным давлением Рф, совпадает с характеристикой по каталогу, построенной для замеренной скорости вращения, вентилятор следует считать соответствующим каталогу. В случае, если фактическая подача Lф не соответствует проектной Lп, то необходимо вторично проверить состояние сети: соответствие ее фактических размеров проекту, засоренность воздуховодов, загрязнение пылеулавливающих устройств, затем исправить сеть. Если точка, определяемая фактической подачей и фактическим давлением, окажется ниже кривой характеристики по каталогу, это означает, что работа вентилятора не соответствует данным, указанным в каталоге (рис. 3.3.5).
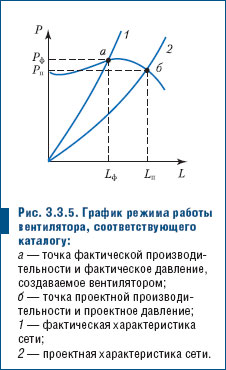
В таких случаях необходимо проверить, соответствует ли фактическая аэродинамическая схема вентилятора каталогу и соответствуют ли условия входа воздушного потока в патрубок вентилятора условиям входа воздуха, принятым при составлении его характеристики, и устранить выявленные дефекты. Если фактический режим работы вентилятора определяется точкой а (рис. 3.3.6), то это означает, что помимо наличия дефектов вентилятора фактическая характеристика сети не соответствует проектной или расчетной, и, следовательно, необходимо выявить и устранить неисправности сети. Отклонение величины полного давления от характеристики по каталогу допускается в пределах ±5 %.
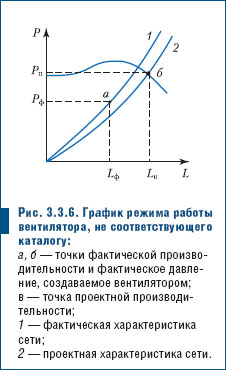
Основные причины, снижающие развиваемое вентилятором давление при определенной частоте вращения колеса вентилятора, и рекомендации по их устранению следующие:
1. Большой прогиб в мягкой вставке на входе в вентилятор
В мягкую вставку вставляют двойное распорное кольцо из стальной оцинкованной проволоки диаметром 2-3 мм. Перекосы в мягких вставках. Перекосы устраняют.
2. Отвод или другие местные сопротивления расположены вблизи всасывающего патрубка вентилятора
При установке отвода на расстоянии одного диаметра от всасывающего патрубка полное давление, развиваемое вентилятором, снижается до 35 % от значения по каталогу. Вентиляционный агрегат устанавливают так, чтобы не было отводов перед вентилятором или чтобы прямой участок перед всасывающим патрубком имел длину не менее 4 диаметров. Если этого сделать нельзя, то в отвод устанавливают направляющие лопатки.
3. Отложение солей, жиров, грязи на лопатках колеса и кожухе вентилятора
Колесо и кожух очищают от загрязнений и предпринимают меры по улавливанию веществ, загрязняющих колесо и кожух. Вмятины или неплотности в кожухе вентилятора устраняют.
4. Вращение колеса в обратном направлении
Направление вращения определяют до испытания вентилятора. Если обнаружено неправильное направление вращения колеса, переключают провода у электродвигателя, поменяв местами любые
два провода в трехфазной подводке. Вопрос о замене вентилятора или изменении его режима работы решается только после регулировки вентиляционной установки. После регулировки повторно измеряют полное давление и подачу вентилятора. Если подача вентилятора, замеренная после регулировки, не будет соответствовать требуемому значению, ее изменяютследующим образом:
- при недостаточной подаче увеличивают частоту вращения колеса вентилятора или заменяют его другим типоразмером;
- при подаче, превышающей необходимую, уменьшают частоту вращения колеса вентилятора или с помощью диафрагмы создают в воздуховоде у вентилятора дополнительное местное сопротивление.
Частоту вращения колеса вентилятора можно увеличить при условии соблюдения допустимой окружной скорости рабочего колеса, а также достаточной мощности установленного электродвигателя. Вентилятор необходимо заменить, если нельзя повысить производительность установки увеличением частоты вращения колеса вентилятора. Если по диаграмме в каталоге режим работы вентилятора оказывается в области низких значений КПД, слева от области экономичного режима работы, то его заменяют
вентилятором того же типа, но меньшего размера и с большей частотой вращения колеса вентилятора. Если по диаграмме в каталоге режим работы вентилятора оказывается в области низких значений КПД, справа от области экономичного режима работы, то его заменяют вентилятором того же типа, но большего размера и с меньшей частотой вращения колеса. Для проверки целесообразности параллельной работы двух вентиляторов на одну и ту же сеть строят их суммарную характеристику.
3.3.6.2. Испытание и регулировка воздухораспределительных сетей
Аэродинамическое испытание вентиляционных сетей производят при полностью открытых дросселирующих устройствах, имеющихся как на общем воздуховоде, так и на всех ответвлениях от него.
Регулирующие устройства, встроенные в конструкции различных воздухораспределителей приточных установок, должны быть полностью открыты.
Если при открытых дросселирующих устройствах электродвигатель вентилятора перегревается, перекрывают дроссель на магистральном участке сети.
При отсутствии дросселирующего устройства между фланцами общего воздуховода на всасывающей или нагнетательной линии устанавливают вставку (диафрагму) из кровельной стали. Дросселирование осуществляют до тех пор, пока сила тока, измеряемая в цепи, не уменьшится до номинального значения, соответствующего мощности электродвигателя, и его перегрев не прекратится. После этого приступают к испытанию сети.
При испытании сети определяют:
- фактические расходы воздуха в основании всех ветвей сети, во всех воздухоприемных и воздуховыпускных отверстиях до и после пылеулавливающих устройств, увлажнительных камер и калориферных установок;
- падение давления в калориферных установках, пылеулавливающих устройствах, увлажнительных камерах и местных отсосах;
- скорость выхода воздуха из приточных отверстий;
- уровень шумов, создаваемых вентиляционной системой.
Расход воздуха регулируетсяс помощью дросселирующих устройств или диафрагм, устанавливаемых между фланцами.
Регулировка сети может осуществляться следующими способами:
1. Последовательным уравниванием отношений фактических и требуемых расходов воздуха;
2. Постепенным приближением к заранее заданному отношению фактического и требуемого расхода воздуха;
3. Уравниванием отношений фактических и требуемых расходов воздуха с использованием характеристик участков сети.
Первый способ применяют при регулировке разветвленных сетей, отсутствии условий для установки дросселирующих органов и невозможности измерения потерь давления в ответвлениях.
Второй способ применяют для малоразветвленных сетей с небольшим числом вентиляционных отверстий и при наличии условий для установки дросселирующих органов и замера потерь давления в ответвлениях.
Третий способ применяют в тех случаях, когда регулирующие органы установлены на прямых участках воздуховодов на расстоянии не менее четырех-пяти диаметров за местным сопротивлением и не менее двух диаметров до последующего местного сопротивления, а также если есть возможность замерить сопротивления всех ответвлений.
На практике вентиляционные сети, позволяющие использовать последний способ регулировки, встречаются редко, поэтому рассмотрим первый и второй методы.
1. Регулировка способом последовательного уравнивания отношений фактических и требуемых расходов воздуха
Регулировку по этому способу осуществляют в два этапа: регулировка по отверстиям каждого ответвления и по ответвлениям сети.
Процесс выполняется в такой последовательности:
- открывают регулирующие устройства на ответвлениях, приточных и вытяжных отверстиях;
- в двух наиболее удаленных от вентилятора отверстиях одного ответвления сети с помощью регулирующих устройств устанавливают отношение фактических расходов воздуха, равное требуемому, по формуле:

где L1ф, L2ф — фактические расходы через первое и второе отверстия соответственно, м3/ч;
L1ТР, L2ТР — требуемые расходы воздуха через первое и второе отверстиясоответственно, м3/с.
Принимая два отрегулированных отверстия за одно, получаем равенство:

где L3ф и L3ТР — фактический и требуемый расходы воздуха через третье отверстие, м3/ч.
Последующие отверстия регулируют, исходя из условия равенства:
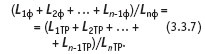
Отрегулировав все ответвления по отверстиям, производят регулировку по ответвлениям сети.
Регулировку начинают с двух наиболее удаленных от вентилятора ответвлений, в которых устанавливают
расход воздуха, отвечающий отношению:
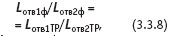
где Lотв1ф, Lотв2ф — фактические расходы воздуха в первом и втором ответвлениях соответственно, м3/ч;
Lотв1ТР, Lотв2ТР — требуемые расходы воздуха в первом и втором ответвлениях соответственно, м3/ч.
Остальные ответвления регулируют таким же методом.
2. Регулировка способом постепенного приближения к заранее заданному отношению фактического и требуемого расхода воздуха
При этом способе учитывается, что производительность вентиляционной установки после регулировки снижается на 10-20 %. Поэтому регулировку производят по соотношению:

где Lф и LТР — фактическая и требуемая производительность вентиляционной установки.
Вначале устанавливают предварительное (приближенное) соответствие расхода воздуха по ответвлениям сети заданному отношению, а затем производят такую же приближенную регулировку по отдельным отверстиям каждого ответвления. После этого вновь проверяют и корректируют распределение воздуха по ответвлениям и по отверстиям. Работу продолжают в такой последовательности до тех пор, пока расхождение между отношением фактического расхода воздуха к требуемому в каждом отверстии не превысит допустимого.
После регулировки вентиляционной сети определяют изменившуюся подачу и полное давление, развиваемое вентилятором. Если подача вентилятора не соответствует требуемой, необходимый расход воздуха может быть обеспечен согласно приведенным указаниям.
По материалам книги Г.В. Нимича, В.А. Михайлова, А.С. Гордиенко, Е.С. Бондаря «Автоматизация систем вентиляции и кондиционирования воздуха»