В настоящее время внутренние водопроводы устраивают с использованием труб из стали, меди, полиэтилена (простого и сшитого), поливинилхлорида (непластифицированного и хлорированного), полипропилена, полибутена и акрилнитрил-бутадиенстирола. Важнейшим элементом водопроводов, как показывает практика, являются соединения труб между собой, с соединительными частями, различными приборами и арматурой. Полимерные трубные изделия следует соединять в такой технологической последовательности: разметить и отрезать трубную заготовку требуемой длины, подготовить соединяемые поверхности к сборке, произвести сборку соединения. Разметку полимерных труб следует производить способами, аналогичными используемым при разметке стальных труб. При этом разметочный инструмент, оставляющий на поверхностях полимерных труб риски или надрезы, использовать не допускается. Резку полимерных труб следует производить ножовками для резки металла, мелкозубыми ручными пилами по дереву, труборезами, а при резке труб под углом использовать соответствующие диаметрам шаблоны (стусла). При использовании дисковых пил для резки труб из полиолефинов (ПВД, ПНД, ПП и ПБ) частота вращения диска должна составлять 33–50 с–1 и для труб из НПВХ, ПВХ‑Х, АБС — 10–13 с–1. (Для резки труб в условиях заготовительных предприятий следует использовать разметочно-отрезные устройства, труборезы, электроприводные ножовки и т.п.). При резке отклонение от плоскости реза не должно превышать для труб диаметром 0,5 мм до 50 мм, 1 мм — 50–110 мм, 2 мм — 160 мм. Подготовку мест соединения на трубных изделиях следует производить с учетом используемого в данный момент способа соединения — контактная стыковая, раструбная или муфтовая с ЗН, склеивание, механические соединения и др.
Подготовка трубных изделий из полиолефинов к сварке начинается с проверки сопроводительной документации на трубы (данных сертификата). Марка, материал и качество полимерных труб должны соответствовать требованиям, принятым в проекте. Затем на специально оборудованной площадке (летом) или в помещении с положительной температурой (зимой) трубы осматривают и подбирают их по диаметрам, толщинам, партиям поставки. Трубы с дефектами — трещинами, задирами, царапинами глубиной более 0,5 мм — отбраковывают. Трубы с овальностью более допустимой (10 %), ведущей к смещению кромок при сборке более чем на 10 % от толщины стенок, но не более 1,2 мм, исправляют с использованием механической либо механопневматической калибровки. Трубы с трещинами или другими повреждениями на концах могут быть использованы после удаления поврежденных участков путем их резки на длине 50 мм. Для соединения отбирают трубы из одной партии поставки, что позволяет уменьшить влияние свойств материала на качество сварки и подобрать трубы со стабильными размерами. Следующий этап подготовки труб к сварке — очистка концов труб от грязи, масел, краски, а также поверхности труб снаружи и внутри на расстоянии от конца не менее чем на 30 мм. Грязь удаляют водой с применением волосяных щеток и последующей протиркой поверхности ветошью до сухого состояния. Соскабливать загрязнения металлическими щетками и инструментом не допускается. Затем концы труб обезжиривают ацетоном либо уайт-спиритом. Поврежденный и подвергшийся воздействию солнечной радиации поверхностный слой выравнивают и снимают (толщина удаляемого слоя 1–2 мм) зачисткой торцов (торцовкой) путем обрезки или фрезерования острым инструментом или специальными устройствами. Торцы зачищают перед сваркой (но не ранее чем за 6–8 ч до сварочных работ), чтобы свариваемые поверхности не окислялись и не загрязнялись. Контактную стыковую и раструбную сварку выполняют путем нагревания до расплавления материала с последующим сдавливанием соединяемых поверхностей и охлаждением стыка под давлением. Контактную сварку выполняют при температуре воздуха не ниже –10 °С для ПНД и ПВД и 0 °С — для ПП и ПБ. Контактную стыковую сварку производят в следующей технологической последовательности. После подготовки трубы укладывают в центрирующее устройство и выравнивают относительно друг друга, далее между трубами вводят нагревательный элемент для оплавления их торцевых поверхностей. Затем трубы отрывают от нагревательного элемента и, после его удаления, трубы сопрягают оплавленными торцами под давлением, выдерживая их до полного охлаждения (происходит формирование сварного шва). Торцы обрабатывают до получения зазора между трубами диаметром: до 110 мм — 0,5 мм и 160 мм — 0,7 мм. Температуру нагревательного элемента, при которой достигается высокое качество сварки, следует поддерживать в ограниченных пределах (табл. 1). 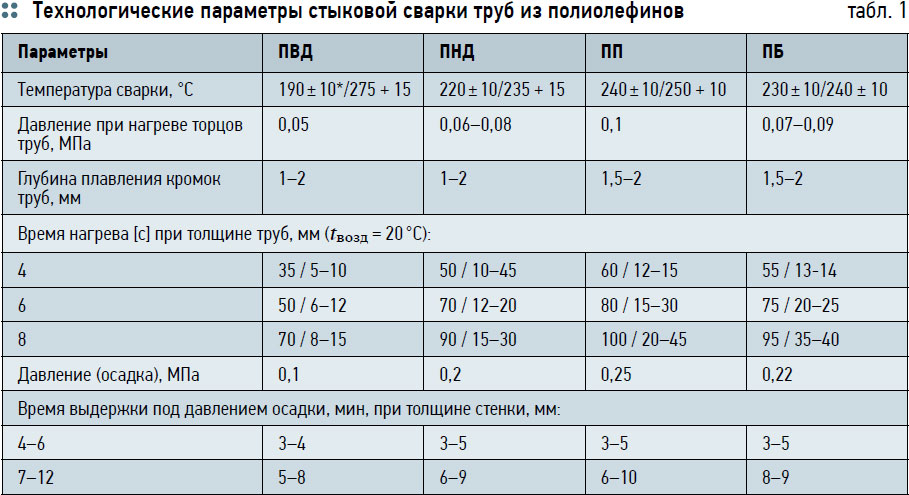
Оплавление торцов труб производят путем плотного и равномерного их прижатия к нагревательному элементу. Время нагрева зависит от толщины стенки трубы и материала. Давление при нагреве поддерживают до тех пор, пока не будет достигнут полный контакт между свариваемыми поверхностями и инструментом. С появлением грата из расплавленного материала давление постепенно снижают, а нагрев продолжают до образования валика высотой 2–2,5 мм при толщине стенки трубы до 5 мм и не более 3–3,5 мм при большей толщине. После окончания оплавления трубы разводят и извлекают элемент, а затем не более чем через 2–3 с (технологическая пауза сварки) после того, как извлекли инструмент, плотно соединяют оплавленные концы труб (осадка трубы). Трубы прижимают одна к другой под давлением осадки 0,1–0,25 МПа, при этом образуется прочный шов. При увеличении давления осадки, указанного выше, оплавленный материал выдавливается из шва, что ведет к ухудшению качества сварки. Сварное соединение охлаждают, не снижая давления осадки, в течение 3–10 минут в зависимости от толщины стенки и вида материала труб. При охлаждении не допускается перемещать и вращать концы труб в зоне сварного шва, а также охлаждать сварной шов водой или снегом. Для обеспечения поддержания расчетных значений технологических режимов и получения качественных соединений стыковую сварку следует производить с использованием ручных либо механизированных сварочных устройств. Ручные сварочные комплекты (устройства для центровки и торцовки и нагревательный элемент) целесообразно использовать в малоудобных местах (подвалах и т.п.). Контактную раструбную сварку выполняют в технологической последовательности, показанной на рис. 1. После подготовки концов трубных изделий дорн нагревательного элемента вводят в раструб одного трубного изделия, а в гильзу нагревательного элемента вводят гладкий конец другого трубного изделия. Для этого нагревательный элемент помещают между концами соединяемых трубных изделий так, чтобы дорн находился напротив раструба, а гильза — напротив гладкого конца трубы. Сближая трубные изделия таким образом, чтобы они плотнее соприкасались с нагревательным элементом, производят требуемое оплавление соединяемых поверхностей. Процесс оплавления продолжают до тех пор, пока у кромок раструба и на трубе по всему периметру не появится валик оплавленного материала высотой 1–2 мм. Внутренний диаметр раструба на трубе (соединительной части) должен быть меньше наружного диаметра гладкого конца трубы. Раструб и гладкий конец быстро надвигают на нагревательный элемент. Время нахождения концов труб на нагревательном элементе должно обеспечить равномерное оплавление всей площади соприкасающихся поверхностей трубных изделий. После этого быстро раздвигают соединяемые трубные изделий и удаляют нагреватель из зоны соединения. 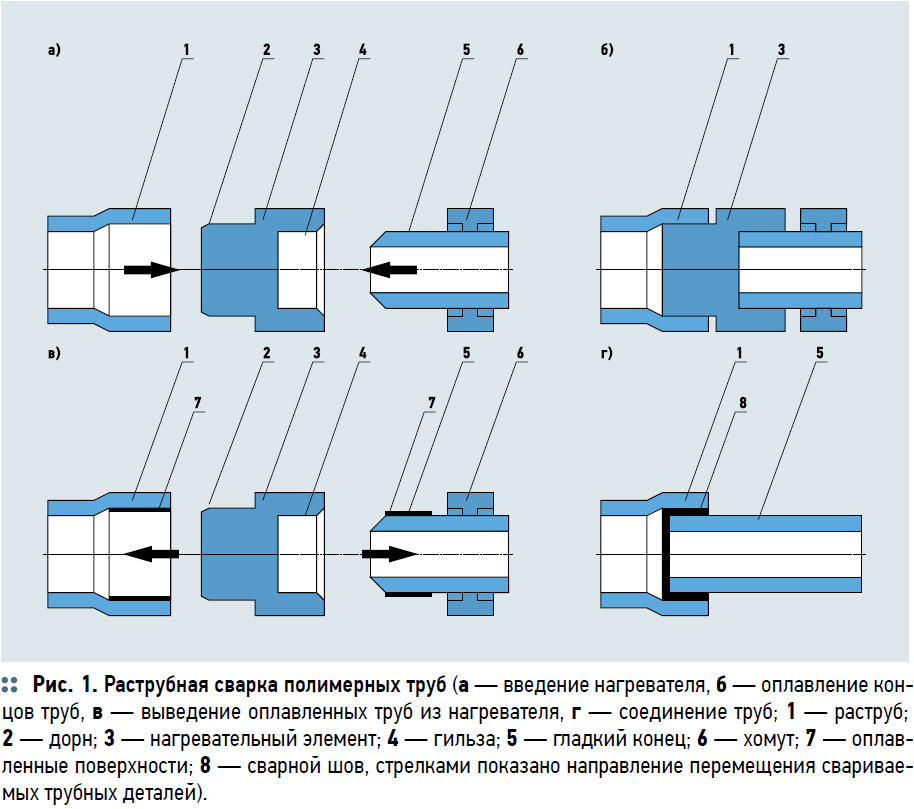
Затем не более чем через 2–3 с, трубные изделия соединяют, вводя гладкий конец в раструб и выдерживая их под осевой нагрузкой в течение 20–30 с в неподвижном состоянии до охлаждения. Основным способом соединения напорных труб и соединительных частей из НПВХ, ПВХ‑Х и АБС между собой является склеивание раструба одного изделия с гладким концом другого. Трубные изделия из НПВХ, ПВХ‑Х и АБС могут склеиваться с получением соединений с требуемой прочностью только при использовании зазорозаполняющих клеев на сильных растворителях. Такие клеи допускают использование только таких трубных изделий, в которых между сопряженными раструбом и гладким концом не будет зазора более 0,6 мм. Прочное склеивание трубных изделий из НПВХ, в которых между сопряженным раструбом и гладким концом зазора менее 0,2 мм, может обеспечиваться при использовании клеев, состоящих из перхлорвиниловой смолы (14–16 маc. частей) и слабого растворителя, например, метиленхлорида (86–84 мас. частей). Для получения прочных клеевых соединение склеивание рекомендуется производить при температуре окружающего воздуха не ниже 5 °С в следующей технологической последовательности: разметить посадочную длину, подготовить склеиваемые поверхности (на гладком конце одного трубного изделия и в раструбе другого), нанести клей на указанные поверхностей, произвести сопряжение раструба и гладкого конца путем вдвигания их друг в друга. Разметку посадочной длины производят линейкой, складным метром и карандашом. Подготовка склеиваемых поверхностей заключается в удалении с них грязи и масел, обработке шлифовальной шкуркой (зашкуривание) с номером зернистости 12–16 (только при использовании клеев на слабых растворителях) и обезжиривании (метиленхлоридом, ацетоном). Клей наносят кистью из натуральной щетины. Сначала клей наносят кистью на внутреннюю поверхность раструба, а затем на гладкий конец. При склеивании труб без зазора клей наносят на 2/3‑х глубины раструба и на всю длину откалиброванного конца трубы равномерным тонким слоем. При склеивании с зазором на раструб наносят тонкий, а на конец трубы — толстый слой. После нанесения клея трубы сразу сопрягают, вдвигая гладкий конец в раструб. Лишний клей, вытесненный из зазора, немедленно удаляют бумажным тампоном. Склеенные стыки в течение 5–10 мин. не должны подвергаться воздействию монтажных нагрузок. Для соединения трубных изделий из НПВХ, ПВХ‑Х и АБС с помощью фланцев или накидных гаек используются буртовые втулки из аналогичных материалов либо концы труб предварительно подвергаются термомеханической обработке. После нагрева концы труб формуются с помощью пуансона, при этом образуются утолщенный бурт или отбортовка. Фланцевые соединения собирают так же, как и на стальных (медных) трубах. Накидные гайки накручивают специальными ключами, которые не деформируют их. Для обеспечения водонепроницаемости соединения уплотняются с использованием резиновых прокладок. Для получения качественных водопроводов из трубных изделий из ППРС их монтаж следует производить с соблюдением требований, изложенных в своде правил СП 40‑101–96. Контактную сварку враструб трубных изделий из ППРС рекомендуется производить при температуре окружающего воздуха не ниже 0°С, а место сварки защищать от атмосферных осадков и пыли. Необходимо тщательно контролировать глубину сопряжения (табл. 2), параметры сварки (табл. 3) и внешний вид сварных соединений (табл. 4). 

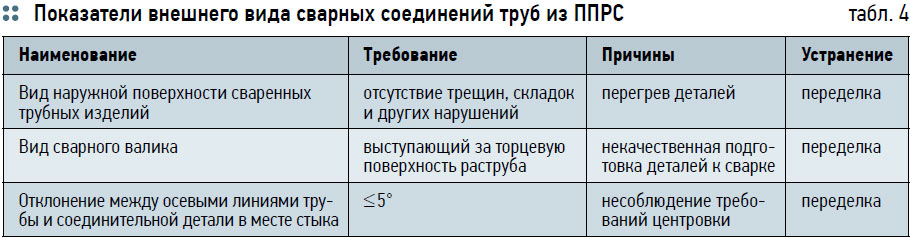
Сборку труб из ПЭ‑С между собой и с латунными соединительными деталями компрессионного типа осуществляется путем обжатия разрезным кольцом трубы на ниппельную часть детали с помощью накидной гайки. Герметичность и надежность соединения достигаются за счет ниппельной части латунной соединительной детали, соответствующего усилия обжатия разрезного кольца к трубе и необходимой пластичности материала трубы. Соединения труб ПЭ‑С с латунными соединительными деталями прессового типа осуществляются путем их обжатия на ниппельной части детали, т.е. при надвигании неразрезного кольца. Соединение трубы ПЭ‑С и латунных деталей компрессионного типа выполняют в следующем порядке: надевают накидную гайку на трубу; надевают разрезное обжимное кольцо на трубу; сопрягают трубу с ниппельной частью соединения и затягивают накидную гайку на резьбовую часть соединения. Трубы из ТПЭ‑С между собой, с арматурой, приборами и трубами из других материалов применяют механические соединения в виде зажимных муфт разной конструкции (они изготавливаются и поставляются на российский рынок приблизительно пятьюдесятью производителями, каждый из которых выпускает их практически по собственной технологии). Общим элементом всех механических соединений указанных труб является штуцер. На него надевается труба, которая обжимается металлическим хомутом с винтом (рис. 2) либо надвижным металлическим или из сшитого полиэтилена (рис. 3), а другой конец штуцера выполняется с резьбой для присоединения к арматуре, коллектору или прибору. 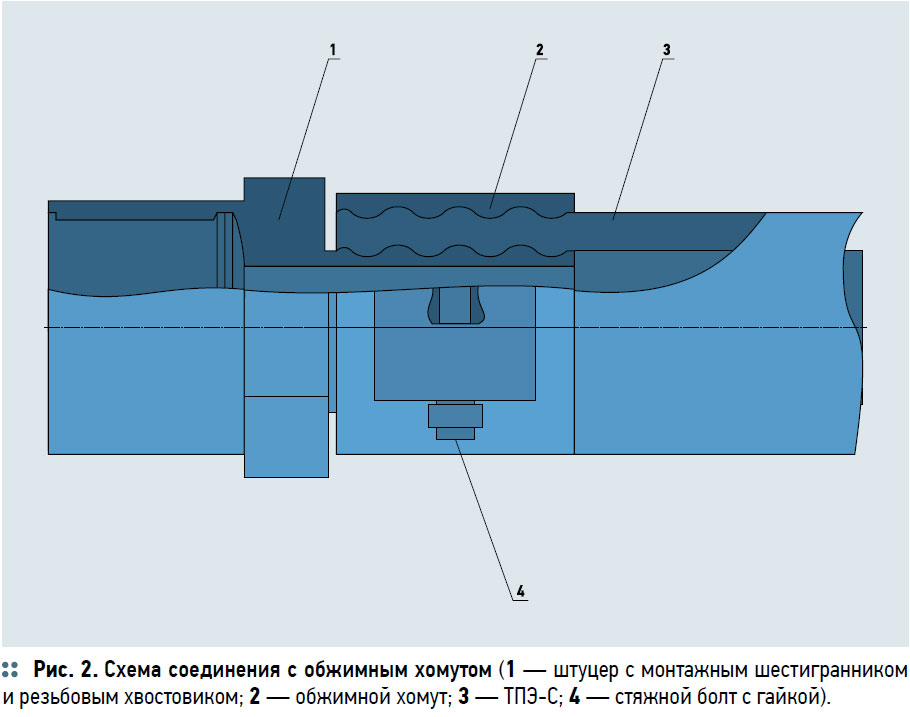
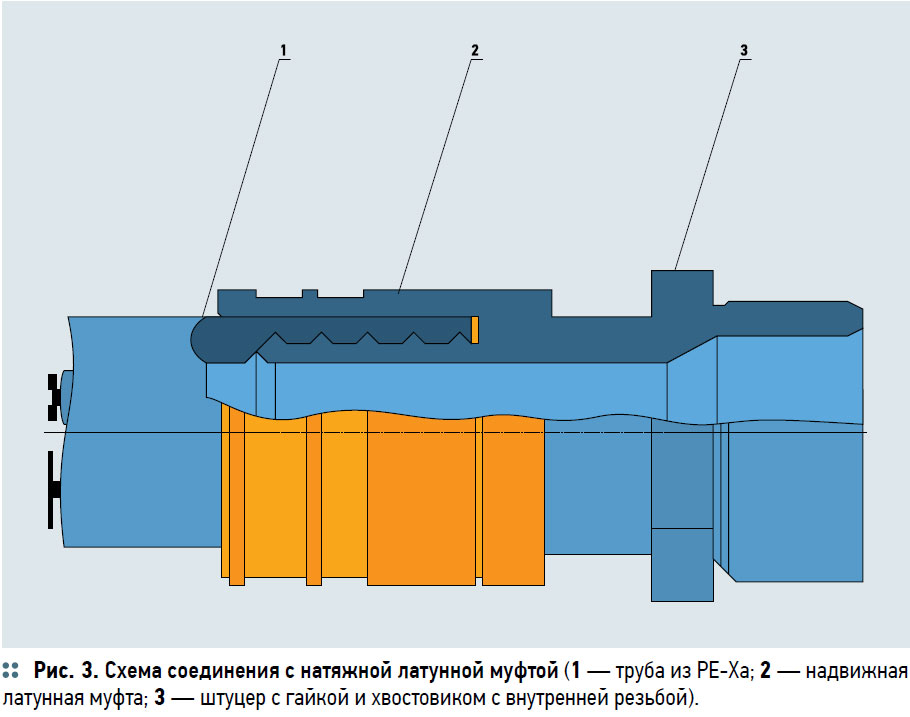
Основным способом соединения труб из хлорированного поливинилхлорида является склеивание с помощью различных клеев гладкого конца одного трубного изделия с раструбом другого (рис. 4). 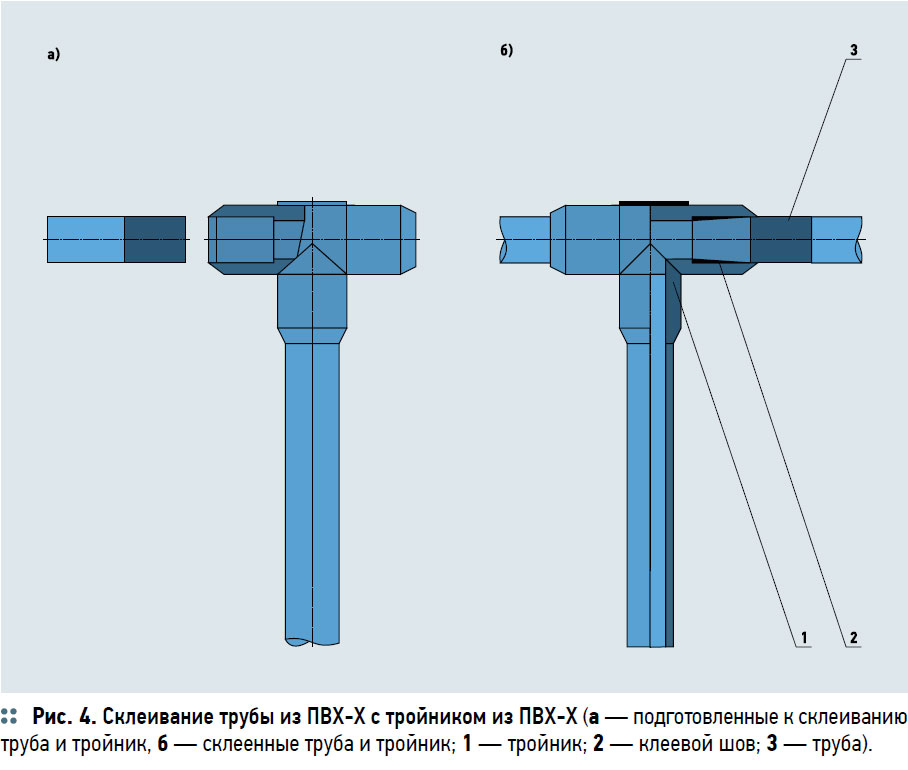
Для устройства разъемных соединений труб из ПВХ‑Х между собой, что необходимо на случай ремонта водопровода, используется сборка с резиновыми уплотнительными кольцами (рис. 5) и фланцевые. 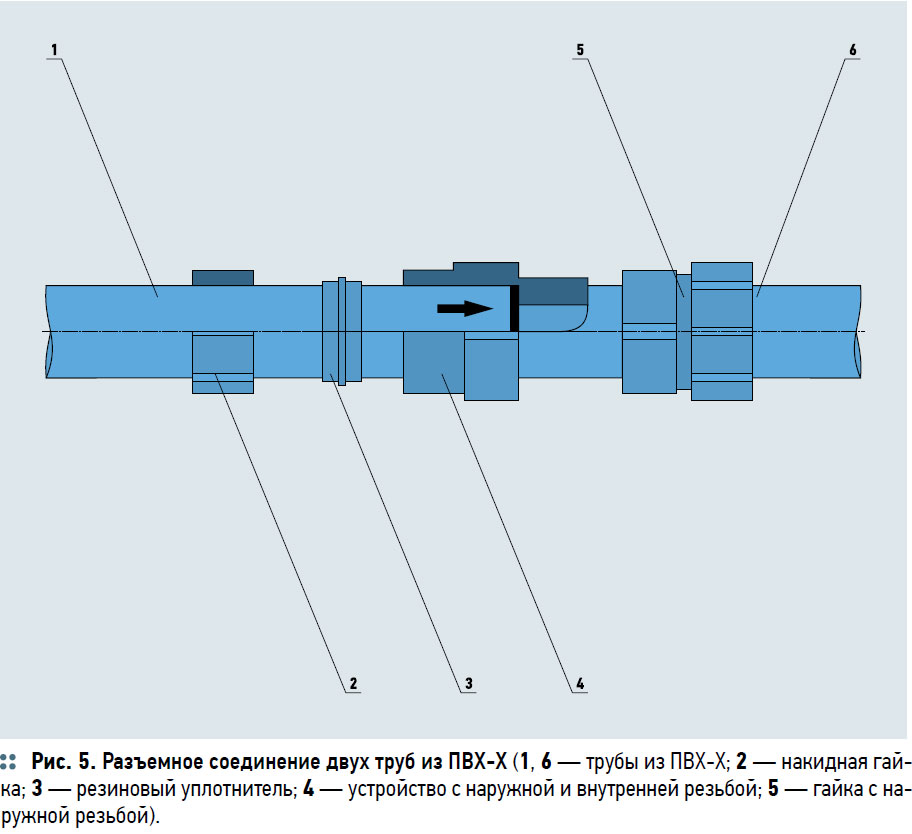
Сборка труб из полибутена между собой и с соединительными частями может осуществляться как сваркой, аналогично полипропиленовым трубам, так и при помощи пресс‑ и резьбовых фитингов, аналогично металлопластиковым трубам, с использованием специального инструмента. В заключение следует заметить, что изложенные в статье положения позволят потребителям успешно использовать не только рассмотренные соединения, но и правильно выбрать, а затем и применить различные типы соединений водопроводных трубных изделий, предлагаемых сегодня на отечественном рынке. 1. СП 40‑102–2000. Проектирование и монтаж трубопроводов систем холодного водоснабжения и канализации из полимерных материалов. Общие требования. 2. СП 40‑101–96. Проектирование и монтаж трубопроводов из полипропилена «Рандом сополимер». 3. СП 40‑103–98. Проектирование и монтаж трубопроводов систем холодного и горячего внутреннего водоснабжения с использованием металлополимерных труб. 4. СП 41‑109–2005. Проектирование и монтаж трубопроводов систем водоснабжения и отопления с использованием труб из «сшитого» полиэтилена. 5. СП 40‑108–2005. Проектирование и монтаж внутренних систем водоснабжения и отопления зданий из медных труб. 6. ГОСТ Р 52134–2003. Трубы напорные из термопластов и соединительные детали к ним для систем водоснабжения и отопления. Общие ТУ. |